A factory contains numerous machines, equipment and systems to ensure efficient and continuous production.The proper operation of these equipments is critical for the smooth running of the work and keeping the production quality high. At this point, the “Maintenance-Repair Department”, which can be called the backbone of the factory, comes into play.
Roles and Functions:
The Maintenance-Repair Department is responsible for ensuring the proper functioning of all equipment, machinery, installations and systems in the factory. Below are the main roles and functions of this department:
- Periodic Maintenance: To carry out regular periodic maintenance of equipment and machinery, to prevent wear and tear and to ensure that malfunctions are detected beforehand.
- Fault Repairs: To quickly eliminate unexpected faults and ensure that production continues with minimum interruption
- Plumbing and Infrastructure Maintenance: To ensure the smooth operation of the plumbing systems of the factory such as water, electricity, ventilation.
- Spare Parts Management: To manage the spare parts needed, to keep the inventory up-to-date and to provide it quickly when necessary.
- Equipment Safety: To take the necessary precautions to ensure the safe and healthy use of equipment and to comply with safety standards.
- Efficiency and Performance Improvements: Monitoring equipment performance, suggesting improvements to increase efficiency, and applying best practices..
Challenges Encountered:
While the Maintenance and Repair Department plays a critical role, it may also face some challenges:
-
Time Pressure: Since the factory must operate uninterruptedly, it can be difficult to find suitable time slots for maintenance and repair work.
With the planning calendar in Flowmio, you can follow all the production processes of your machines or lines and plan the most suitable time interval in advance and add it to your calendar so that your maintenance team is informed of these planned maintenance when the day comes. you can provide.
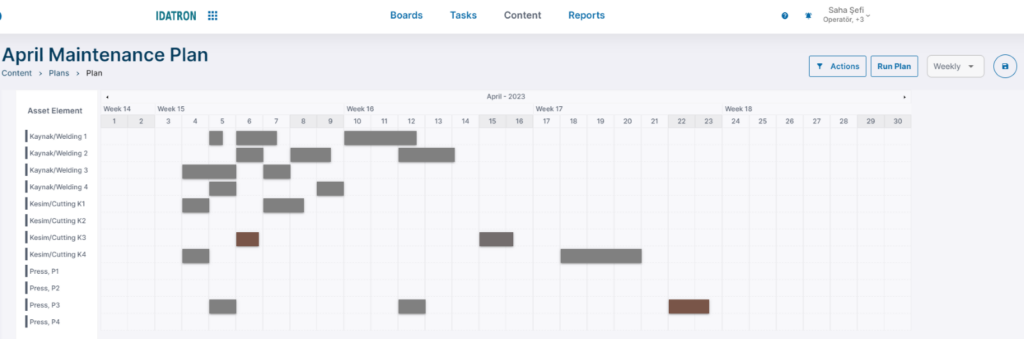
-
Technical Complexity: Evolving technology and complex machinery may require staff to constantly stay up to date.
You can digitally store instructions, documents or SOPs for each machine or maintenance-repair job in FlowMio and access them whenever you need them.
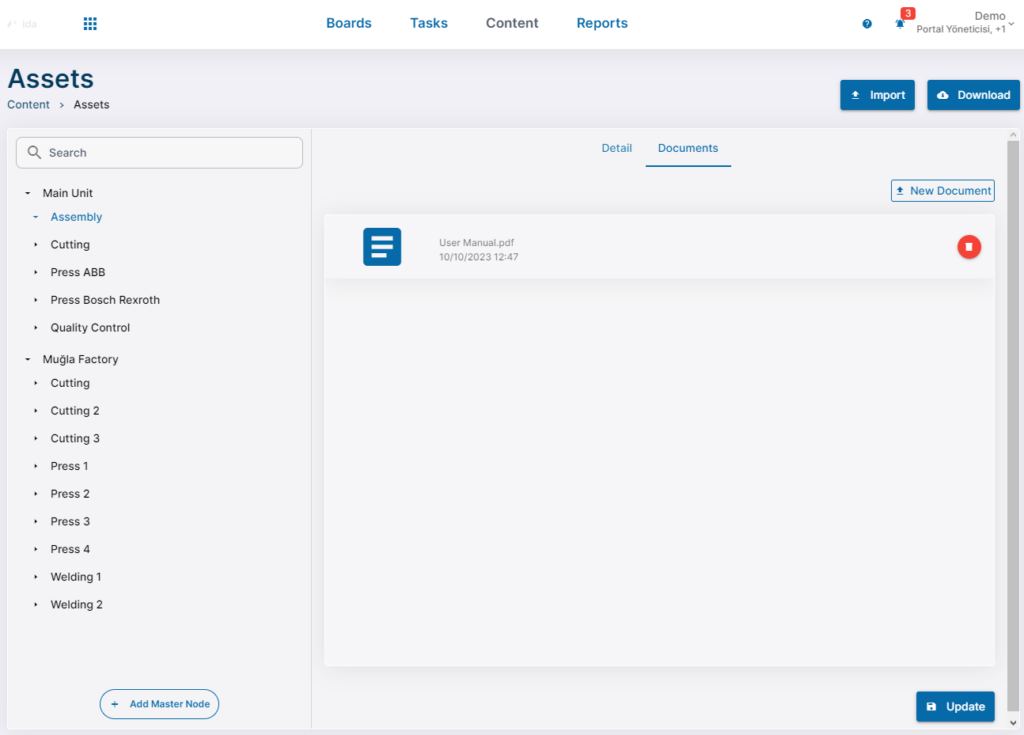
3. Budget Constraints: Maintenance and repairs can be costly. Budgetary constraints can make it difficult to develop optimal maintenance strategies.
But as a result of the analyzes you will obtain from planned maintenance and repairs with FlowMio, you will have the opportunity to maximize your machine efficiency and prevent future malfunctions with a cause-effect relationship.
4. Rapid Response: Rapid response may be required in case of unexpected malfunctions. This may require personnel to be prepared for emergencies.
At this point, you can instantly transmit a fault record created in FlowMio to the entire maintenance team, trigger various alarms, and also prioritize these interventions to achieve optimum operating performance.
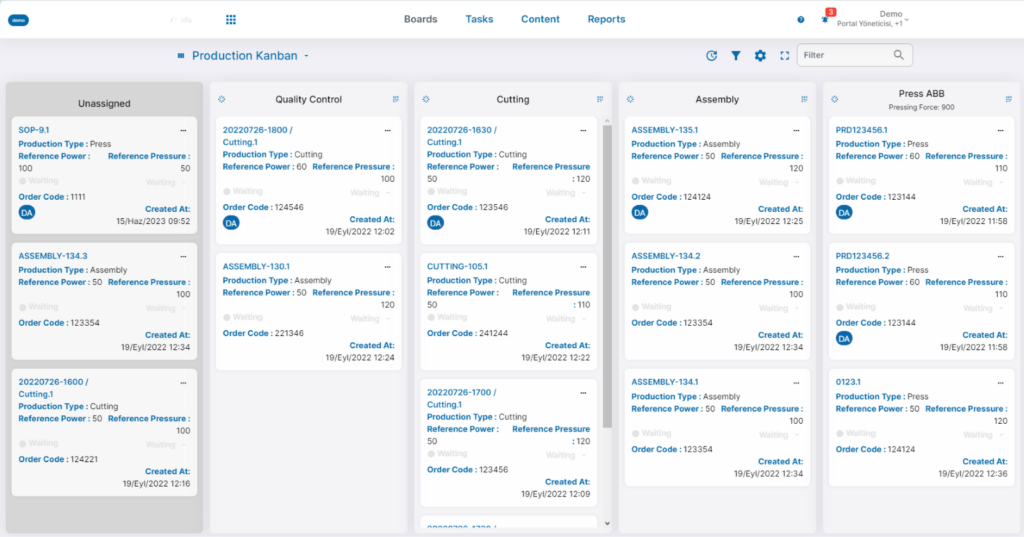
5. Documentation and Monitoring: All maintenance and repair activities need to be properly recorded and monitored. This is important to be able to make decisions based on accurate data.
But it is also the main challenge of carrying out all these activities on paper. FlowMio, on the other hand, stores all actions of a maintenance-repair activity from start to finish in a way that you can access digitally without any time limit. You can require digital SOPs to be followed for the work done and collect photographic evidence. With this data collected for each activity, many visualizations can be made, from MTTR to monthly trend analysis.
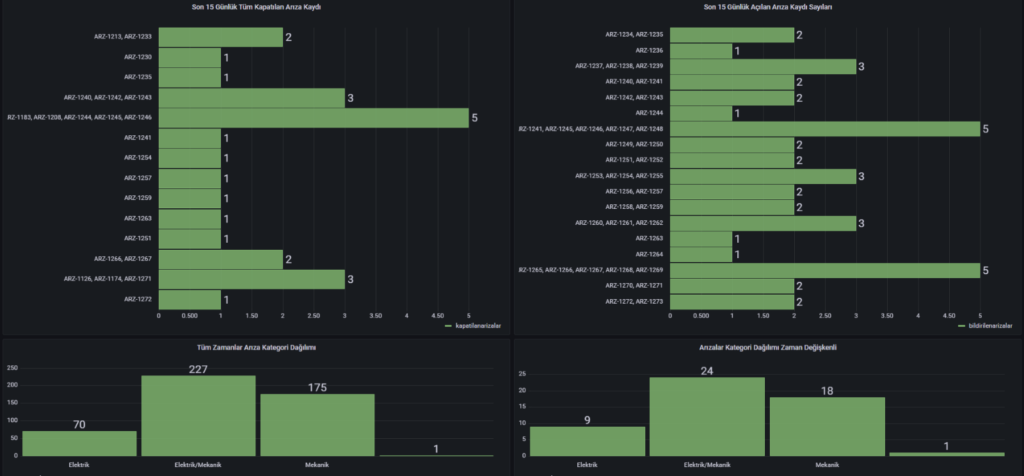
