All Features
Production
Digitize your production processes end-to-end to instantly manage orders and increase operational efficiency. Track performance with its mobile-compatible and flexible structure, and maintain uninterrupted production with rapid interventions.
Asset Management (BOA – Bill of Assets)
FlowMio’s asset management module allows you to take control by digitizing all physical assets in your factory in a hierarchical structure. You can define, locate, and track production lines, machines, stations, equipment, and other resources within a systematic structure.
Seeing all assets within a single digital tree significantly enhances the transparency and sustainability of production processes.
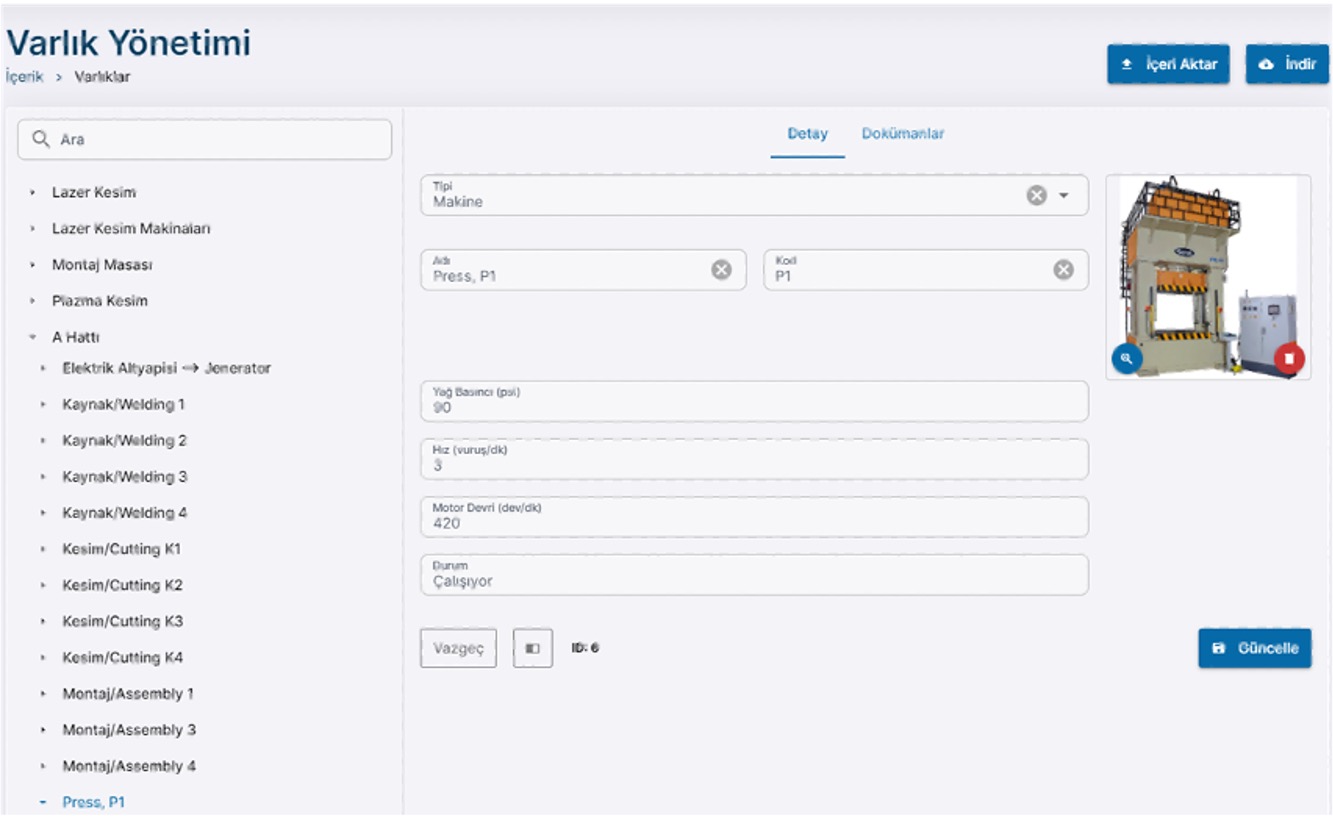
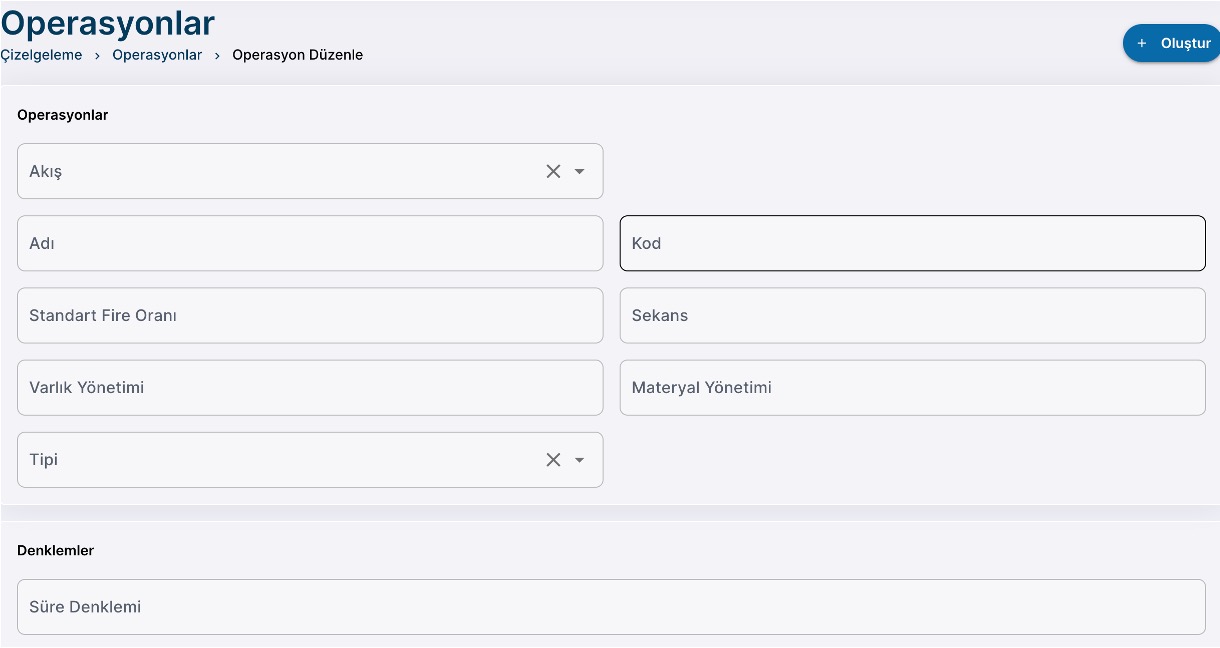
Material Management (BOM – Bill of Materials)
Material management, the heart of production, is under control with FlowMio. Thanks to Bill of Materials (BOM), you can define in detail the raw materials, semi-finished products, and auxiliary materials used in the production of each product.
This structure ensures the integrated progress of all processes, from supply chains to production planning. It minimizes problems arising from stock surplus or shortage by guaranteeing the use of the right amount of material at the right time. At the same time, you can increase your flexible production capability by defining different BOMs according to product versions.
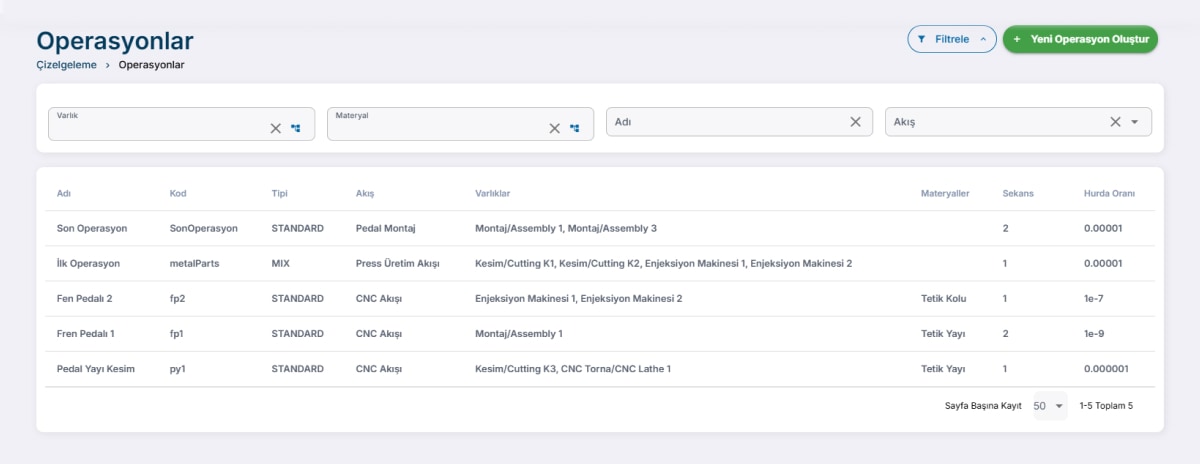
Route/Operation Management
With FlowMio, you can optimize work orders by digitally planning your production routes and operation steps. You can define the operations to be applied for each product and their sequence, detailing the workstation, duration, resources, and personnel information for each operation. Thus, production processes become more efficient, and bottlenecks can be identified and intervened in advance.
Operation management, with its easily adaptable structure even in flexible production systems, provides both high efficiency and flexibility.
Recipe Management
FlowMio’s recipe management feature provides great convenience, especially for process-oriented manufacturing businesses. You can define material components, process parameters, usage rates, and quality criteria for each product in detail. Recipes ensure that both production and quality standards are maintained digitally.
Every change made through the system is versioned and tracked, ensuring traceability and auditability. Thanks to recipe-linked production processes, standard deviations are quickly noticed, non-conformities are prevented, and quality continuity is ensured.
Kanban
FlowMio’s digital Kanban system allows you to visualize and manage the workflow in your production process according to lean manufacturing principles.
It prevents unnecessary stock accumulation by establishing a real-time connection between material flow and production steps. What is being produced, what is waiting, and what is completed at each production step can be monitored instantly.
While operators are easily guided via visual cards, managers can quickly identify system bottlenecks. This structure provides flexibility and increases production agility.
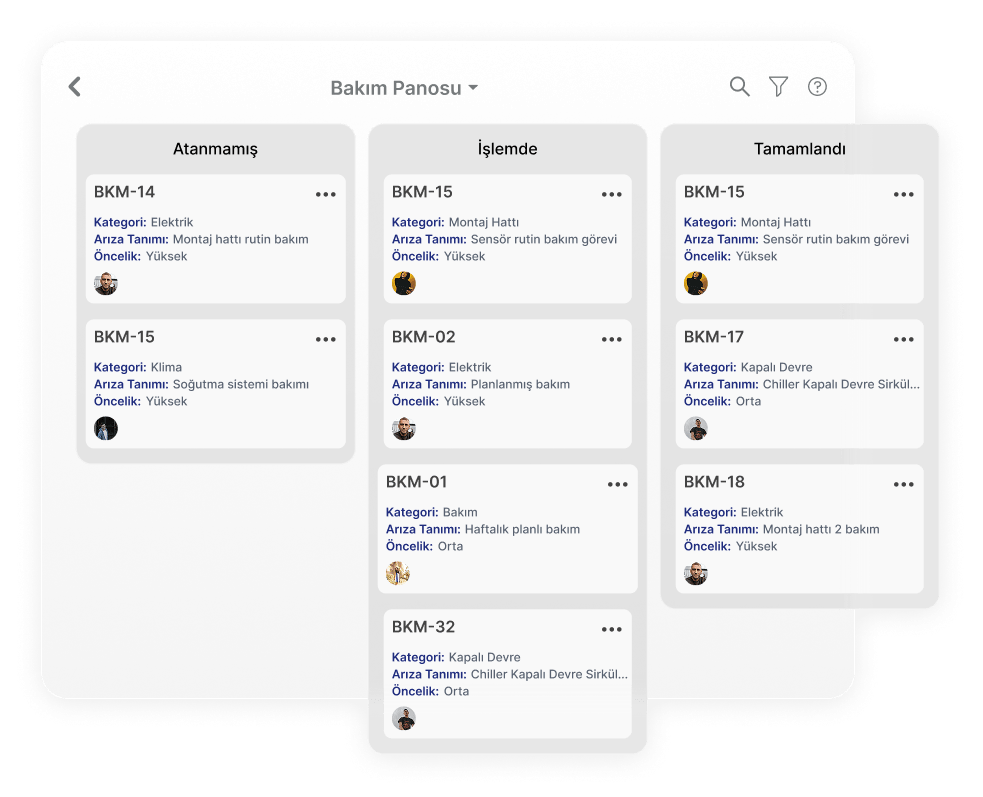
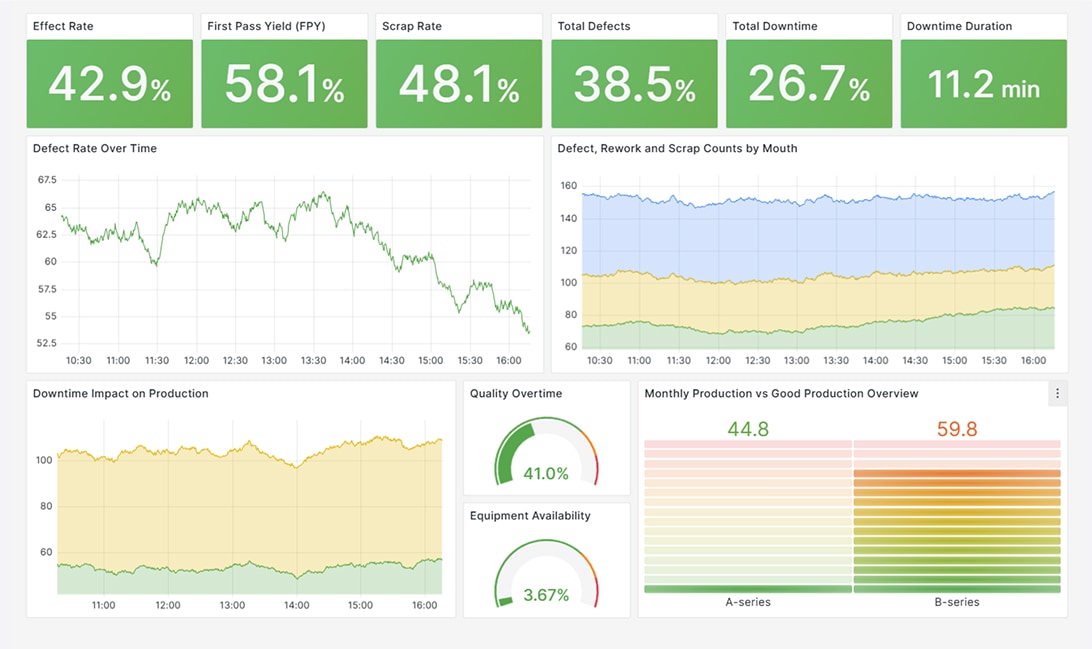
OEE (Overall Equipment Effectiveness) Analysis
With FlowMio, you can track OEE digitally and evaluate your machine efficiency based on three key metrics: availability, performance, and quality. You can view OEE rates instantly for each piece of equipment or production line and perform comparative analyses with historical data. The reasons for efficiency drops are automatically analyzed and reported. This allows maintenance planning, investment decisions, and production improvement efforts to be more data-driven. FlowMio turns OEE tracking into the main tool for operational improvement.
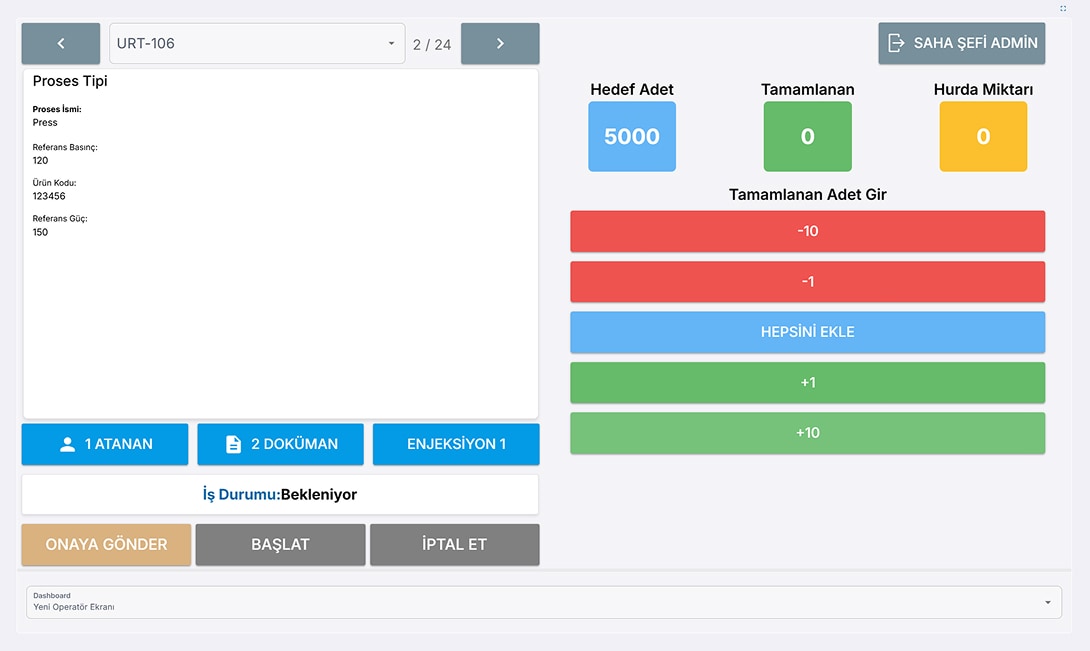
Operator Guidance and Performance Management
FlowMio digitally guides operators, increasing consistency and quality in production processes. Operator screens clearly show which job to do, in what order, and with which parameters. At the same time, performance criteria such as production speed, job completion time, and quality compliance are tracked, allowing for personal or shift-based performance analyses. This system both increases employee engagement and provides managers with a strong control mechanism for achieving production goals.
Production Work Orders
Manage work orders, the most critical step initiating the production process, end-to-end with FlowMio. Digitize the process from order to production to eliminate manual errors, and automatically create work orders according to your production plan. Work order details include all information such as recipes to be used, routes, quantity to be produced, and planned start and end times.
Tasks can be assigned to operators, and the production process can be tracked in real-time. With work order tracking, delays, deviations, and disruptions are reported instantly, enabling quick action.
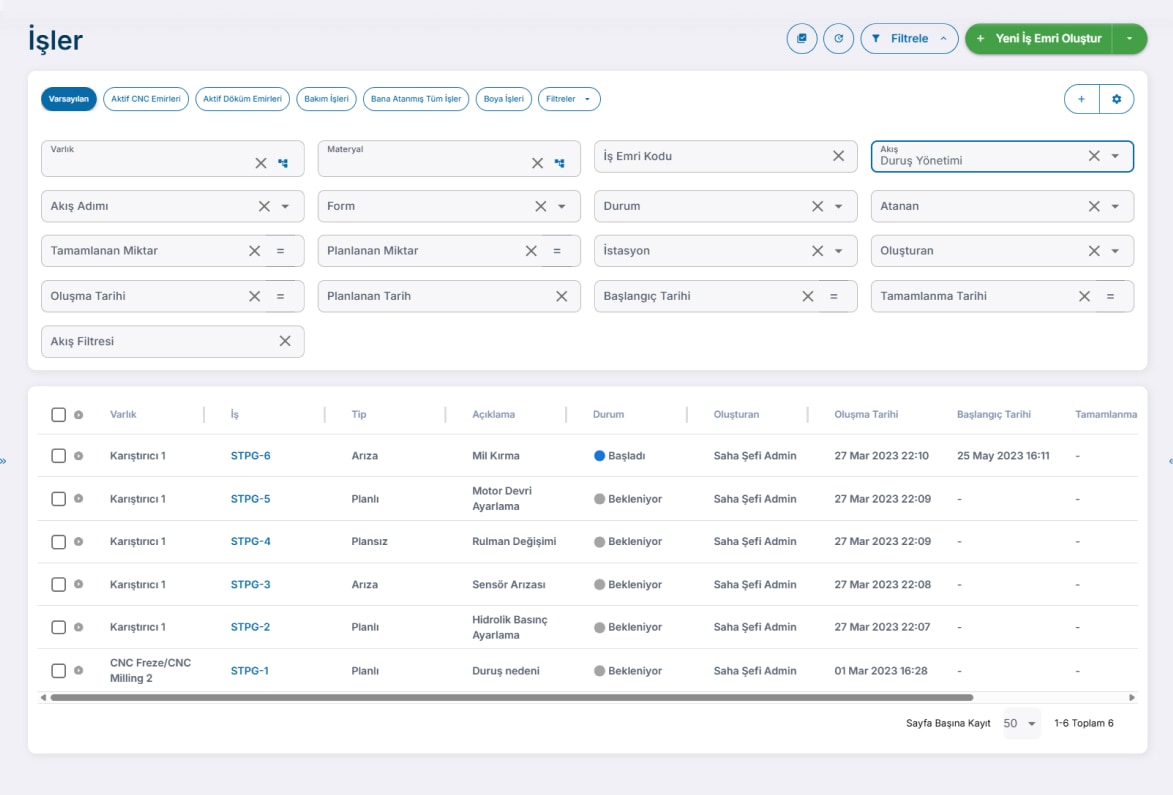
Downtime / Root Cause Management
Digitally tracking planned or unplanned downtimes in production is very easy with FlowMio. The system automatically records the duration and reason for each downtime, and users can classify downtime reasons under specific categories.
Additionally, tools enabling root cause analysis allow for the identification of continuously recurring problems and the development of permanent solutions. This structure increases production continuity, ensures more accurate maintenance planning, and contributes to the improvement of OEE values.
Product Trees
Thanks to FlowMio’s product tree management, you can define in detail each sub-component and production step that constitutes your final products. The entire structure from raw materials and semi-finished products to the final product is shown in a layered manner. It supports product variants and alternative structures, adapting to flexible production models.
It is also used as basic data in production cost calculations. This systematic structure enables you to execute many processes, from material planning to quality control, accurately and quickly.
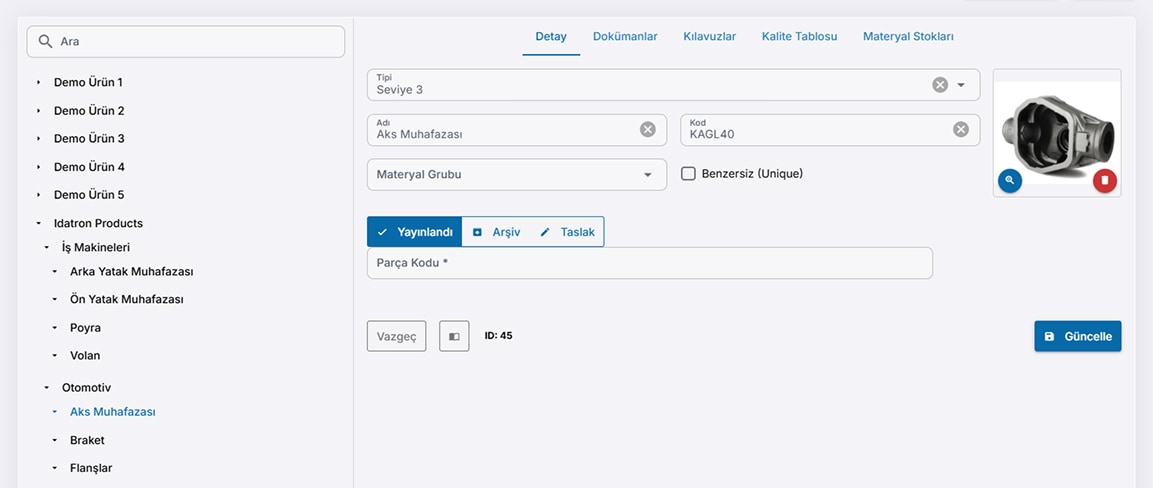
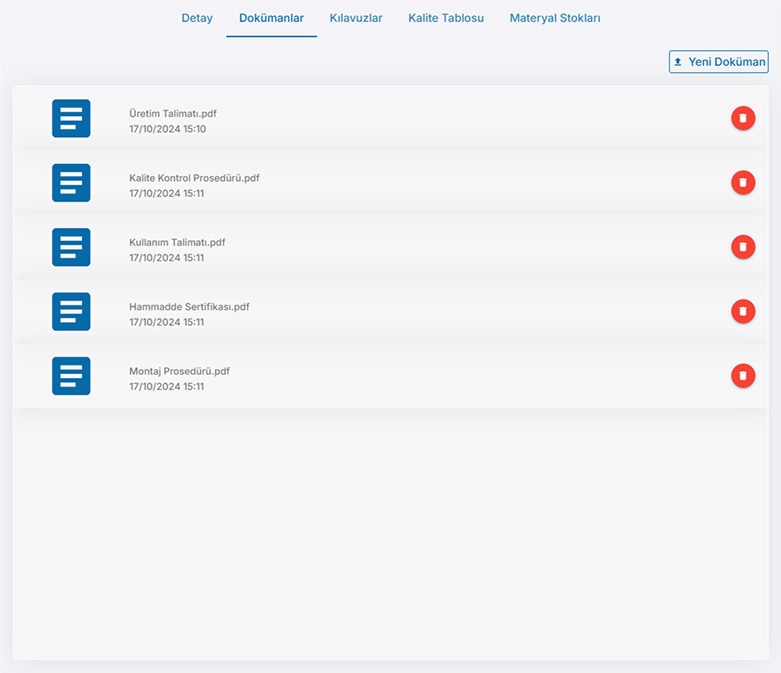
Product Documents and Change Management
Technical documents, quality certificates, user manuals, and technical drawings associated with each product are managed centrally via FlowMio. Thanks to the versioning feature, every change made is recorded in the system, is traceable, and previous versions can be easily reverted to.
Furthermore, changes made to the product are automatically reflected in production recipes and routes, preventing inconsistencies. This module provides a significant contribution in terms of both quality assurance and traceability.
Machine Data Monitoring (Production Dashboards)
FlowMio’s advanced machine data monitoring infrastructure collects real-time data from every machine on the production line and visualizes this data on user-friendly dashboards. Critical information such as production speed, breakdown status, downtime duration, production quantity, efficiency, and goal adherence can be monitored instantly. This allows managers to make quick decisions, maintenance teams to respond immediately to breakdowns, and overall production efficiency to be continuously monitored. The system provides complete control with both historical data and live information.
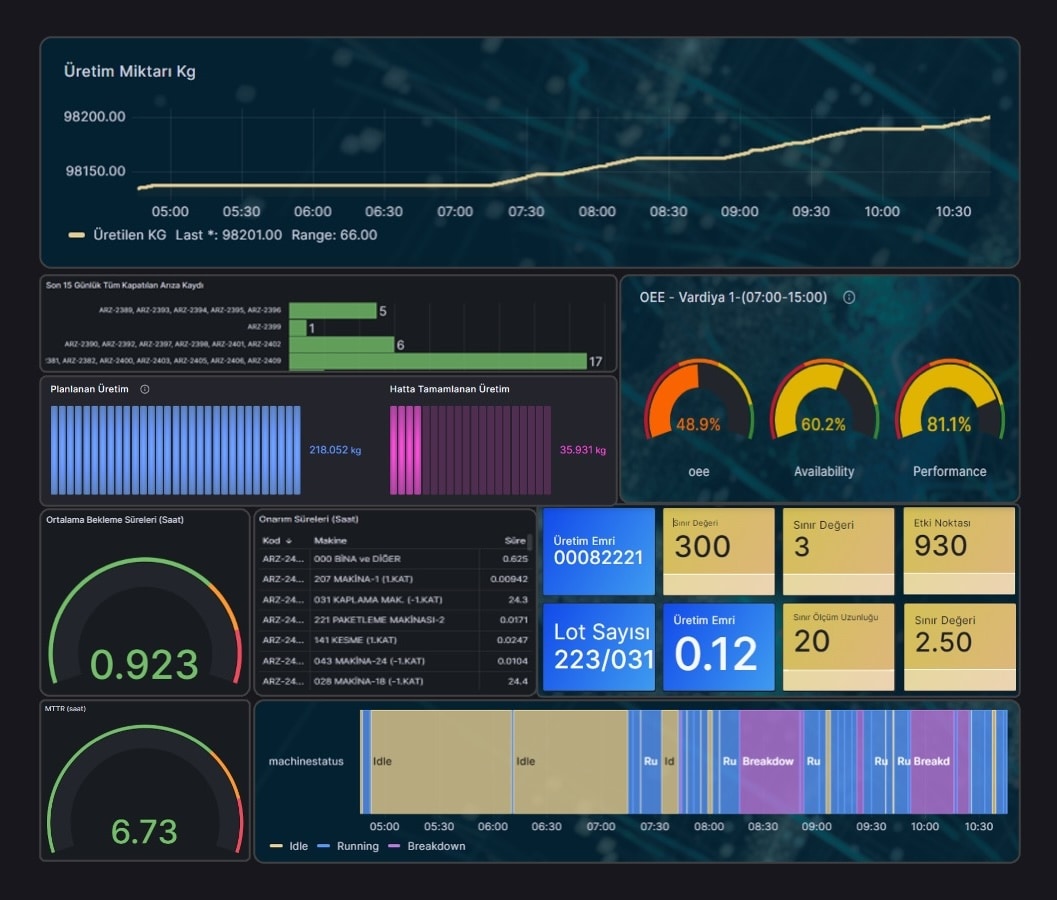
Non-Conforming Product Notifications
Allows for the quick notification and analysis via the system of products that do not conform to the recipe or show deviations during production. FlowMio can automatically classify these products and send instant notifications to the relevant quality, production, or maintenance teams.
This ensures defective products are identified before leaving the production line, root cause analysis can be performed, and the production process can be quickly optimized. It helps maintain quality standards through a continuous improvement approach.
Production Process with Barcode/RFID
FlowMio integrates barcode and RFID technologies to ensure traceability at every step of the production process. All movements from material entry to product exit are digitally recorded. Operators can perform material consumption, operation transitions, and product tracking simply by scanning a barcode/RFID. This system eliminates the need for manual data entry, reduces errors, and ensures rapid data flow. It also directly supports inventory and quality management.
Maintenance
Easily manage breakdown tracking, maintenance plans, and inventory management from a single screen. Work integrated with your team to minimize downtime and increase operational efficiency.
Maintenance Plans
With FlowMio, you can proactively plan maintenance processes to prevent production losses caused by breakdowns. You can define asset-specific planned maintenance scenarios and work integrated with the production schedule to ensure the right interventions are made at the right time.
Managing maintenance plans digitally optimizes resource utilization while also helping to control maintenance costs.
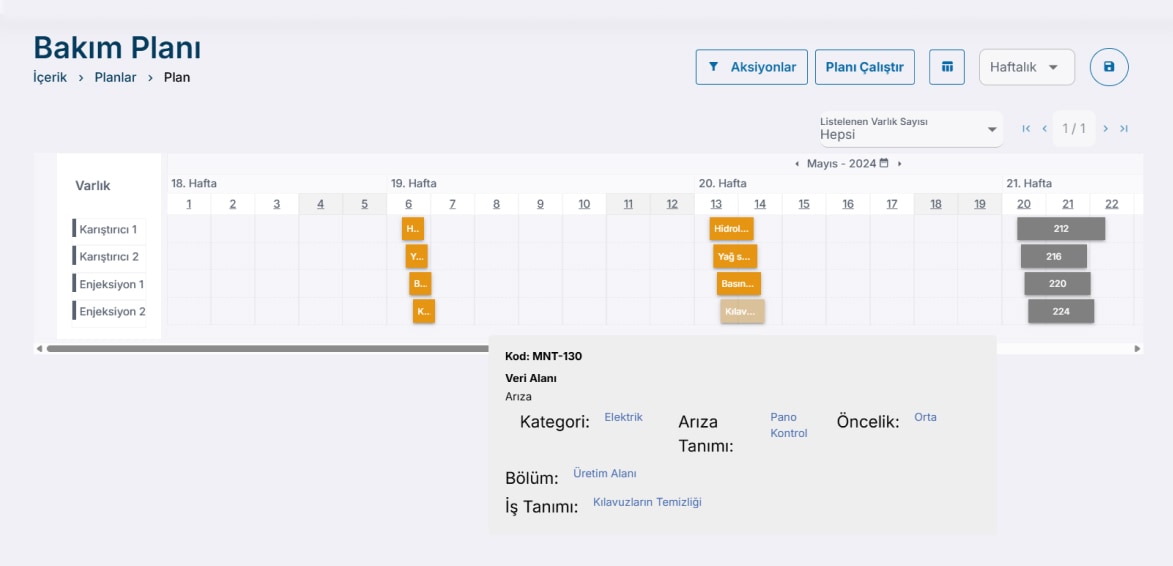
Periodic Maintenance
FlowMio allows you to define time-based or counter-based periodic maintenance for your equipment. With automatic reminders and work orders, periodic maintenance processes are carried out uninterruptedly and on time. This prevents unexpected downtimes while extending equipment lifespan.
Planned maintenance ensures production continuity and increases equipment efficiency.
Autonomous Maintenance
By defining operator-assisted maintenance processes via FlowMio, you can enable teams at the machine to effectively perform daily checks and simple maintenance activities.
Thanks to digital checklists, visual instructions, and an automatic recording system, maintenance operations become standardized, preventing quality deviations. Autonomous maintenance enhances both employee engagement and machine reliability.
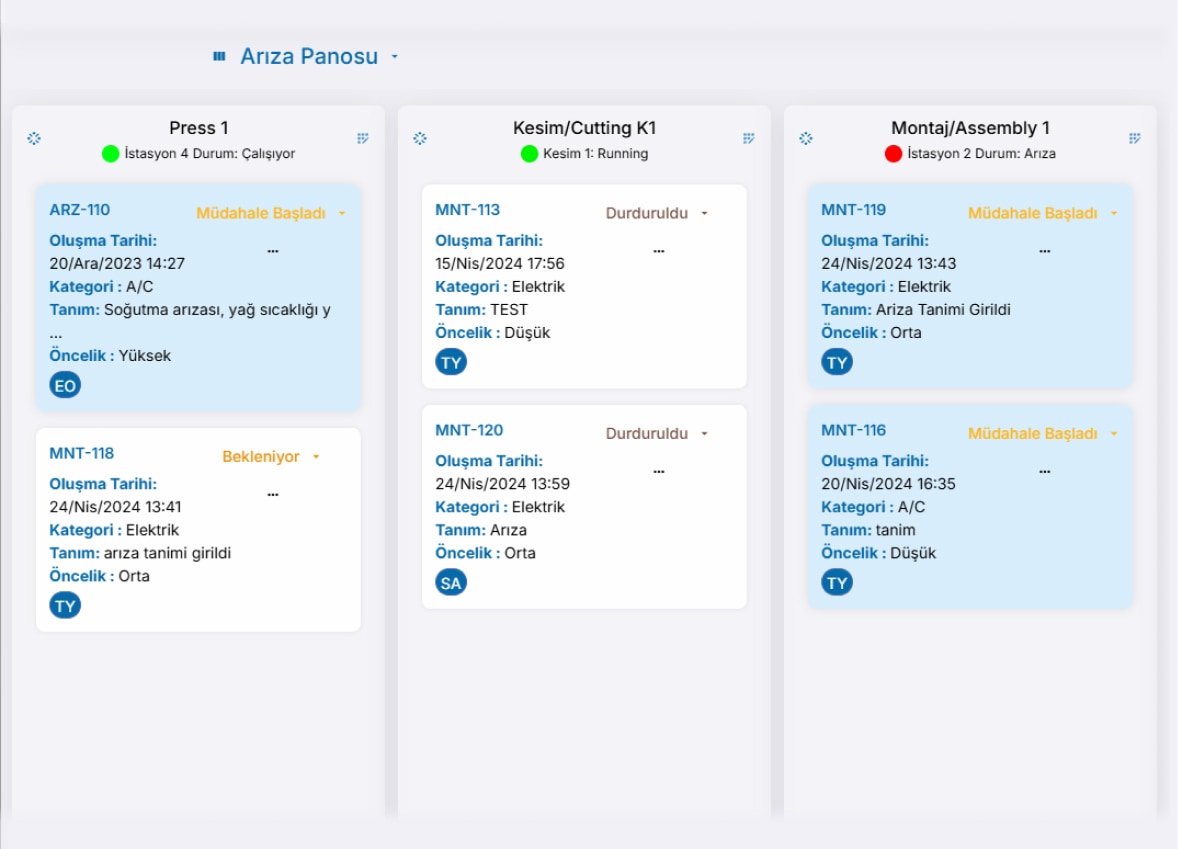
Breakdown Tracking
FlowMio instantly records and classifies breakdowns, comparing them with past records to help you identify recurring problems. All details related to breakdowns — start and end times, intervention teams, spare parts used — are archived in the system.
This enables analysis and easy planning of preventive actions against similar future breakdowns. Breakdown management becomes one of the fundamental pillars of production continuity.
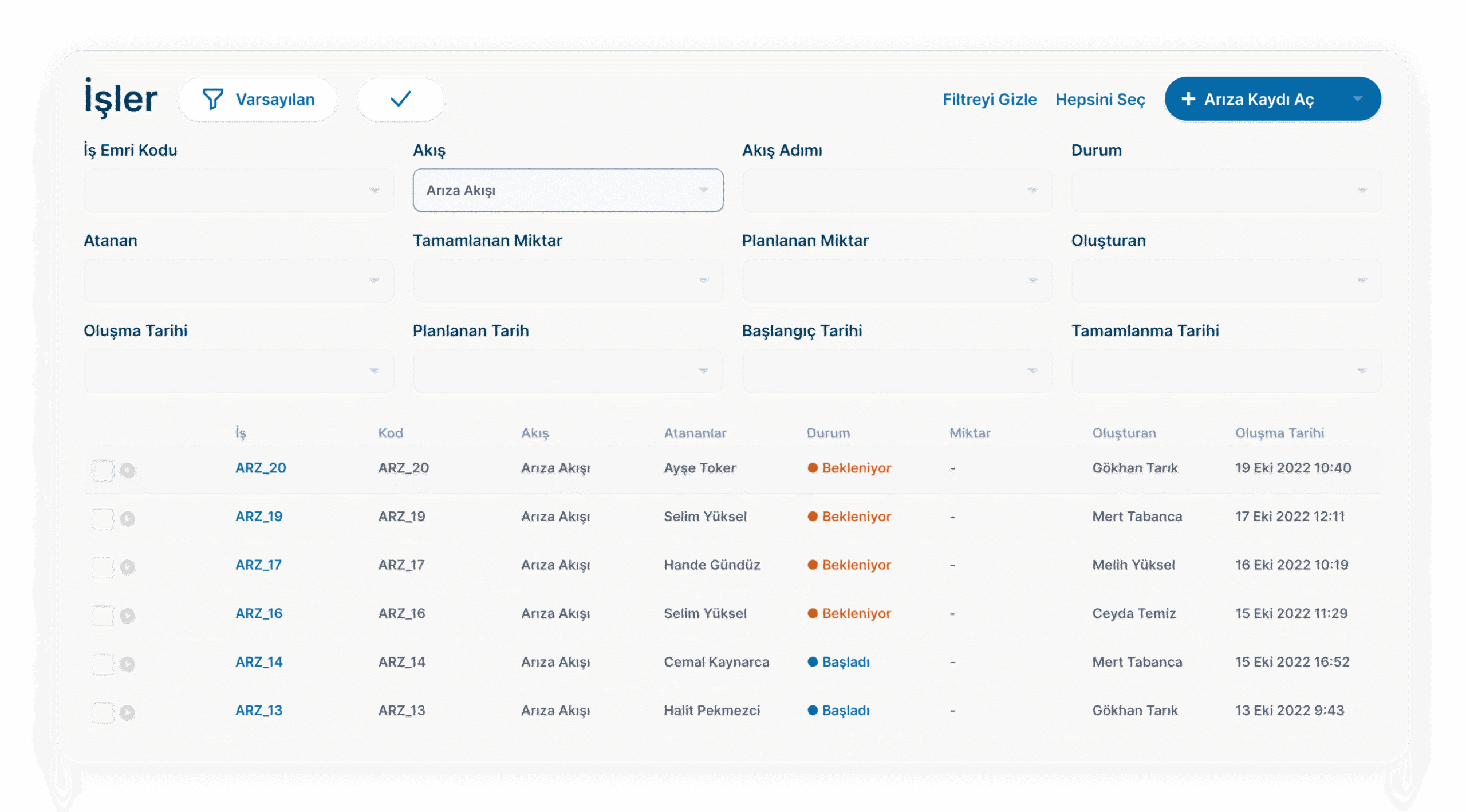
Work Lists
FlowMio creates work lists for maintenance teams to manage their tasks regularly and efficiently. Each task is clearly defined with the responsible person, priority, and date information.
Task assignments can be made on a daily, weekly, or monthly basis, and the workload of teams in the field is distributed evenly. Additionally, completed tasks are reported instantly in the system, ensuring transparency.
Mobile Terminals
Through the FlowMio mobile application, maintenance teams can instantly access the information they need in the field and perform maintenance operations via mobile devices. Actions such as creating breakdown records, completing tasks, and requesting spare parts can be done mobilely. This structure both increases work speed and enables the transition to paperless digital maintenance management.
Mobile Device Management
Thanks to FlowMio’s mobile device management infrastructure, maintenance personnel can receive task assignments, perform data entries, and easily create breakdown notifications via devices defined in the system. The configuration, user authorizations, and security of these devices are managed centrally. Mobile device management accelerates the digitalization of field operations.
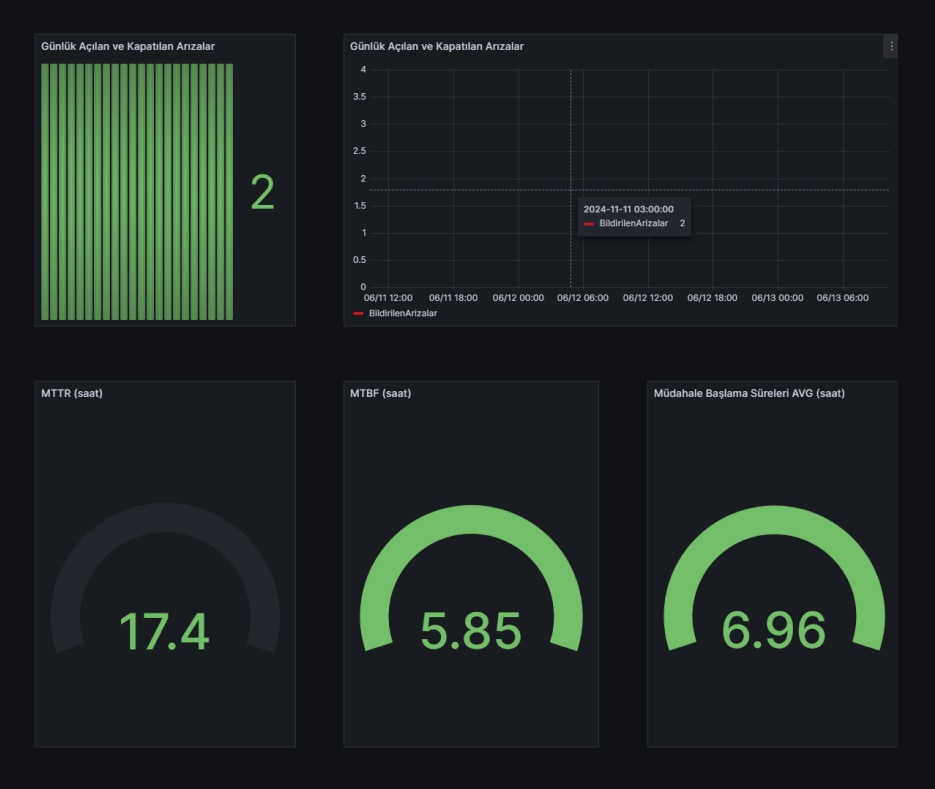
Maintenance Dashboards
FlowMio’s maintenance dashboards visualize all maintenance activities and performance indicators on an equipment basis. Metrics such as actual and planned maintenance durations, breakdown frequency, MTTR (Mean Time To Repair), and MTBF (Mean Time Between Failures) can be tracked instantly.
Managers can make informed decisions based on this data and continuously improve maintenance strategies.
Maintenance - Production Synchronization
FlowMio manages maintenance and production plans in an integrated manner, ensuring both departments work towards the same goal. Maintenance activities on the production line are considered concurrently with the production plan, preventing conflicts.
This minimizes production loss and optimizes the time management of maintenance teams. This integration strengthens collaboration across the factory.
Maintenance Notifications
When machine breakdowns occur, periodic maintenance time approaches, or equipment performance degradation is detected, FlowMio instantly sends maintenance notifications to the relevant personnel.
These notifications appear on both mobile devices and desktop interfaces, allowing the maintenance process to start quickly. The possibility of early intervention minimizes production disruptions.
Quality Control
Standardize your quality control processes, perform data-driven analyses with smart forms, and minimize errors. Ensure quality at every stage of production.
Quality Management System
FlowMio’s quality management system digitizes the quality control points in your production process, offering real-time tracking capabilities. While all quality processes are managed from a single center, internal system controls allow for rapid detection of non-conformities and identification of their root causes. Production compliant with standards is guaranteed through recorded processes.
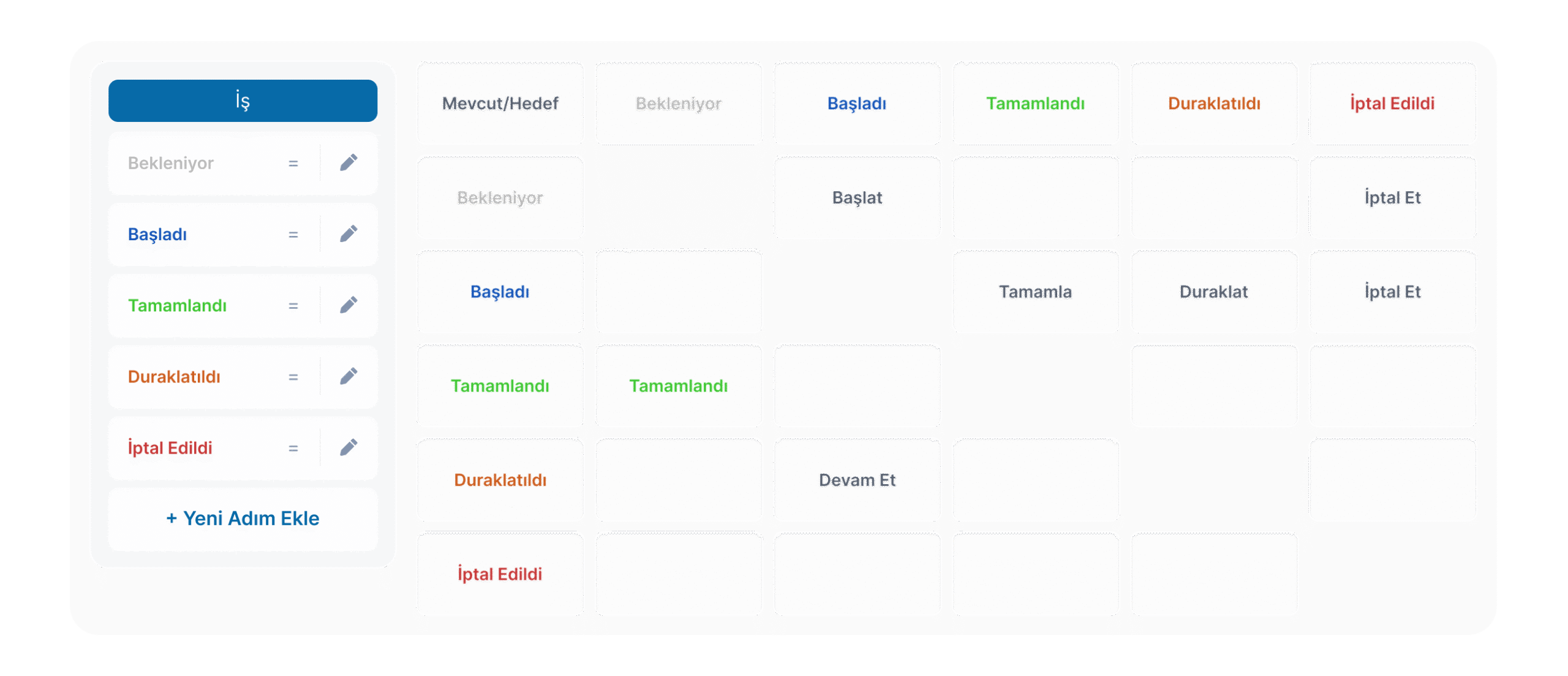
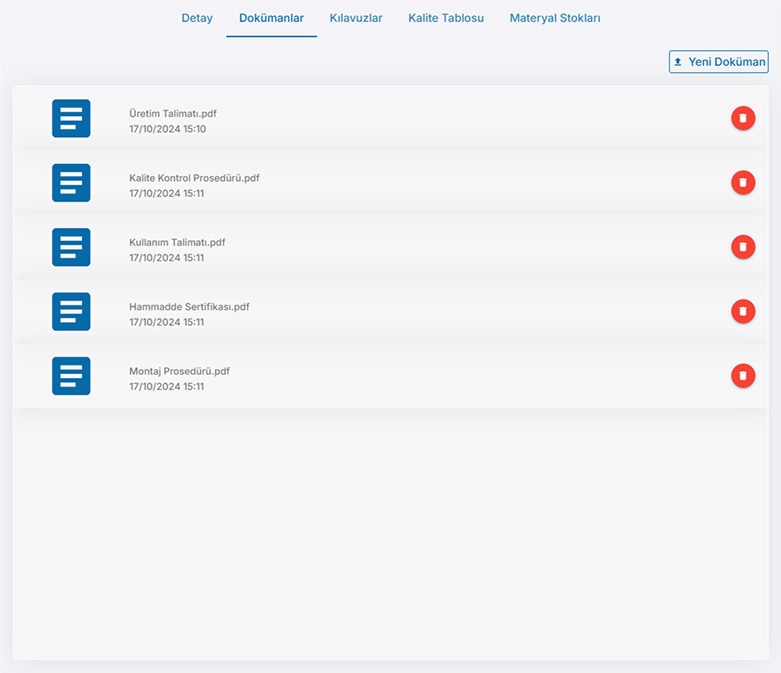
Document Library
All quality procedures, instructions, standards, and records are stored centrally within the digital document library. Access can be granted based on authorizations, allowing employees to instantly reach the information they need. This structure facilitates access to information while also streamlining audit processes.
Revision Tracking
All changes made to quality documents are recorded on a version basis. The revision history can be tracked in detail, and previous versions are accessible. This clearly shows what change was made, when, and by whom, making documentation processes transparent.
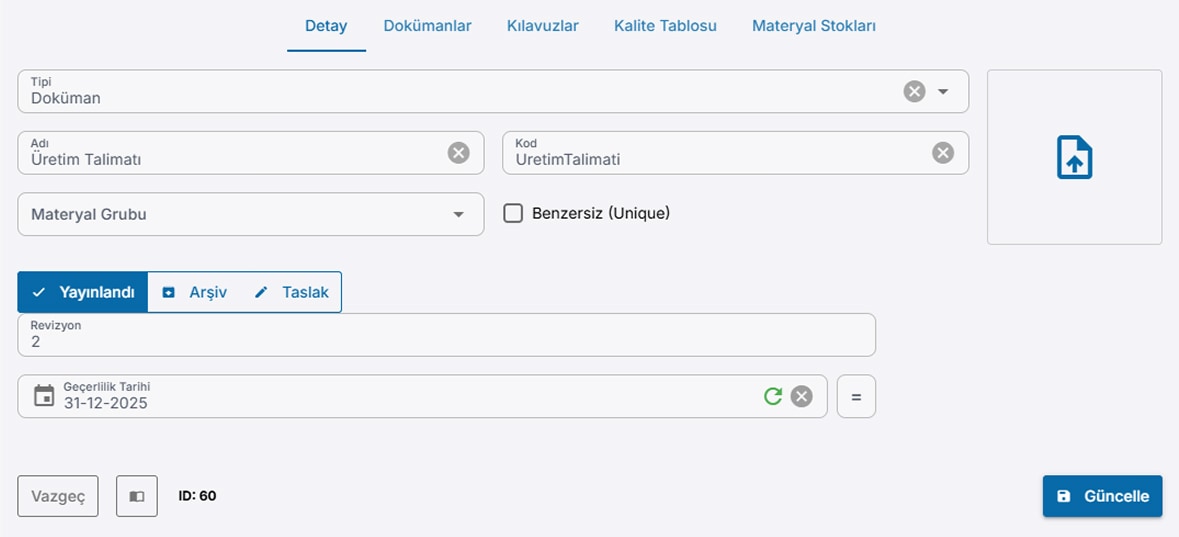
Form and Flow Design
Business-specific quality control forms, control flows, and approval mechanisms can be easily created via FlowMio using a drag-and-drop method. This allows you to design digital flows that perfectly match your internal quality procedures, making your quality processes systematic and measurable.
Matching Quality Documents with Assets and Materials
FlowMio allows you to match quality certificates and technical documents with production assets and materials. This way, the required quality documents for each piece of equipment or product group are defined digitally.
The system alerts you to missing documents or expired certificates, thus preventing quality risks.
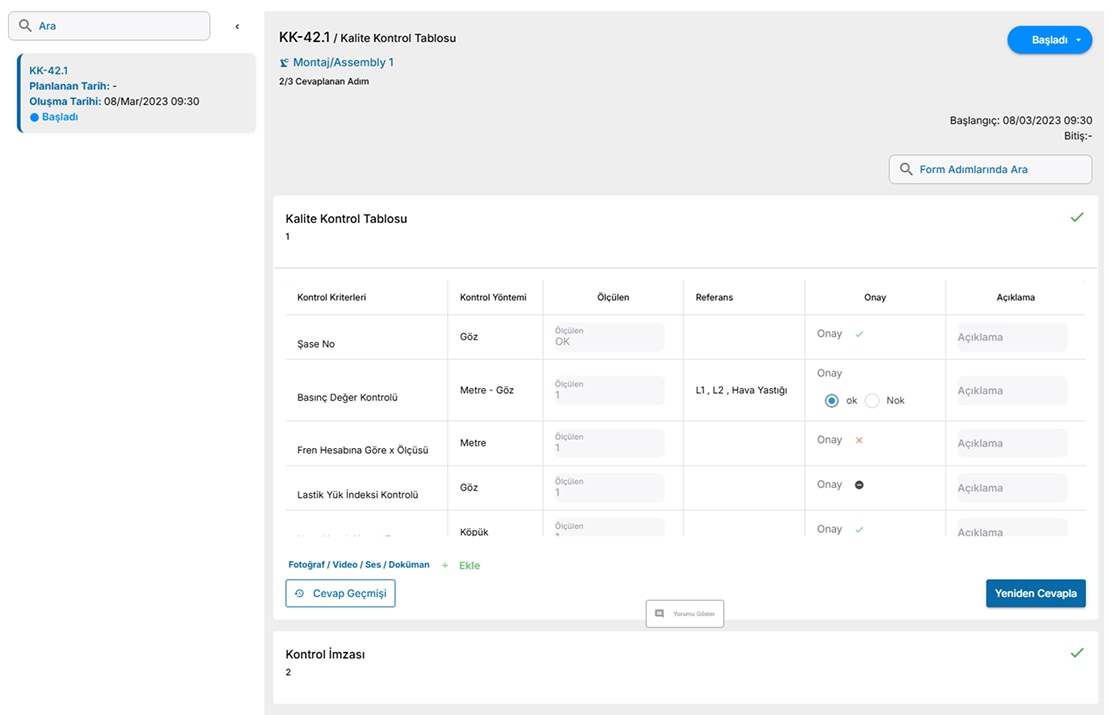
Quality Measurement Forms
Quality control forms are created digitally, suitable for manual or automatic data entry during the production process. All controls—whether product-based, process-based, or shift-based—are systematically carried out using standardized forms.
The collected data becomes analyzable, allowing quality-related decisions to be made based on data.
Measurement Integration
FlowMio works integrated with measurement equipment such as weighing systems and temperature sensors to automatically collect measurement data at quality control points.
This structure both speeds things up and prevents manual entry errors. Real-time data flow enables rapid detection of deviations.
Information Retrieval with OCR
Thanks to FlowMio’s OCR (Optical Character Recognition) feature, data from paper-based quality documents, measurement forms, or certificates are automatically transferred to the digital environment. This feature reduces the archiving burden while preventing data loss due to manual entry. It offers significant speed and convenience in your digitalization process.
Quality Notifications
In cases of non-conformity, measurement deviation, or document deficiency, the system instantly generates a notification. Relevant personnel are alerted via mobile devices or desktop. Thanks to the notification system, errors can be addressed immediately, protecting product quality and increasing situational awareness.
Quality Control with Mobile Devices
Quality teams can perform their inspections directly on-site using tablets or smartphones. Digital forms can be filled out, photos can be attached, and deviations can be entered into the system instantly.
Thanks to this flexibility, quality controls are conducted in real-time and without interruption.
Non-Conformity Tracking
FlowMio records all non-conformities detected during production or final product checks in detail. The type, source, intervention method, and results of the non-conformity can be tracked in the system. Root cause analysis can be performed, and recurring quality problems can be prevented.
Material Quality Criteria
Quality criteria for raw materials and semi-finished products are defined in the system, moving incoming material checks to the digital environment. Material acceptance/rejection decisions based on checks against defined criteria are recorded. This ensures quality assurance at the beginning of the process and prevents non-conforming materials from entering production.
Planlama
Optimally plan your production, maintenance, and quality processes with dynamic scheduling supported by smart algorithms. Make your workflow efficient, manage your schedule, and advance your operations without disruption.
Production Plan
FlowMio facilitates the creation of production plans based on orders and capacity. Optimal planning is achieved by considering product priorities, deadlines, work centers, and resources. Every step from the beginning to the end of the production process can be tracked, and plan deviations are detected in real-time, enabling rapid intervention.
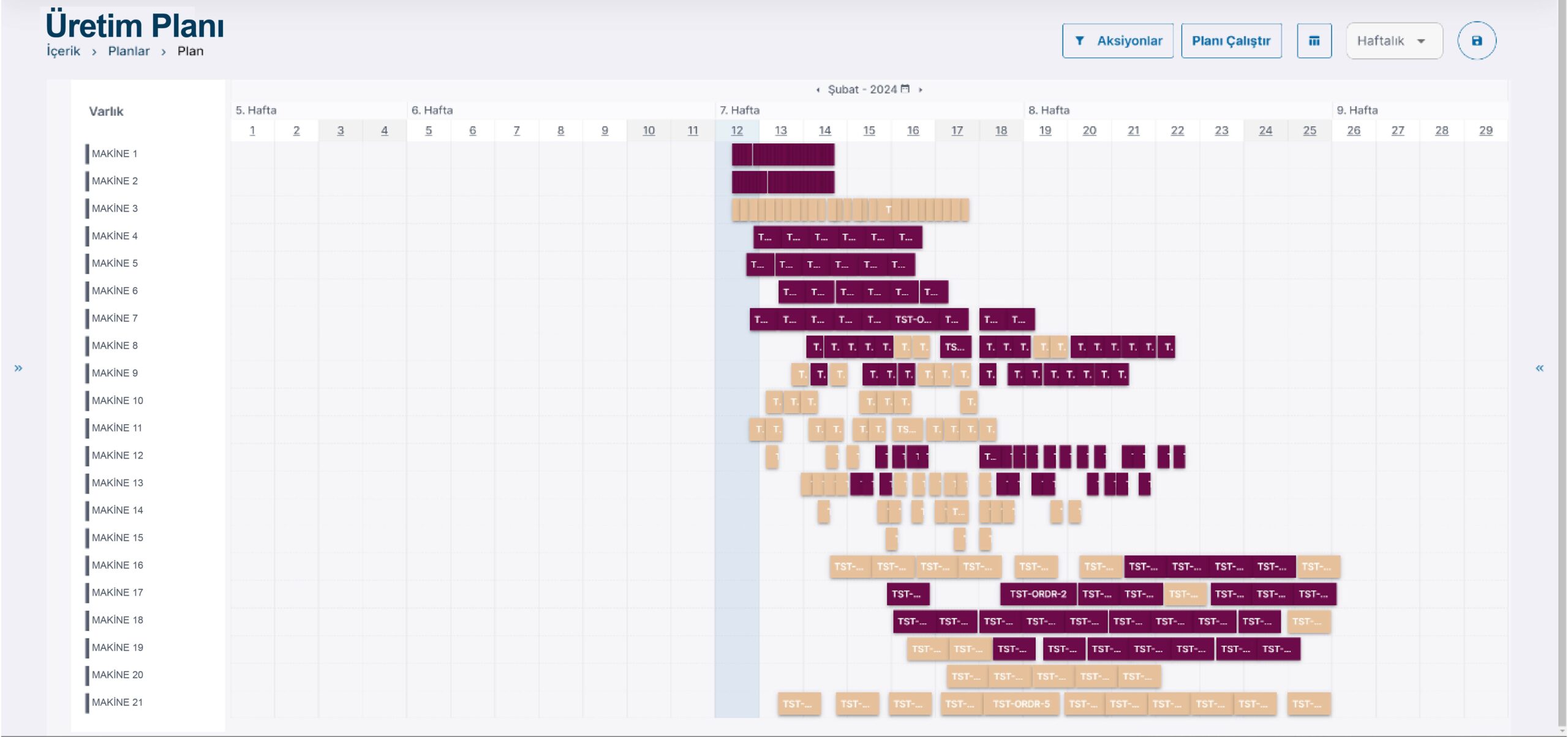
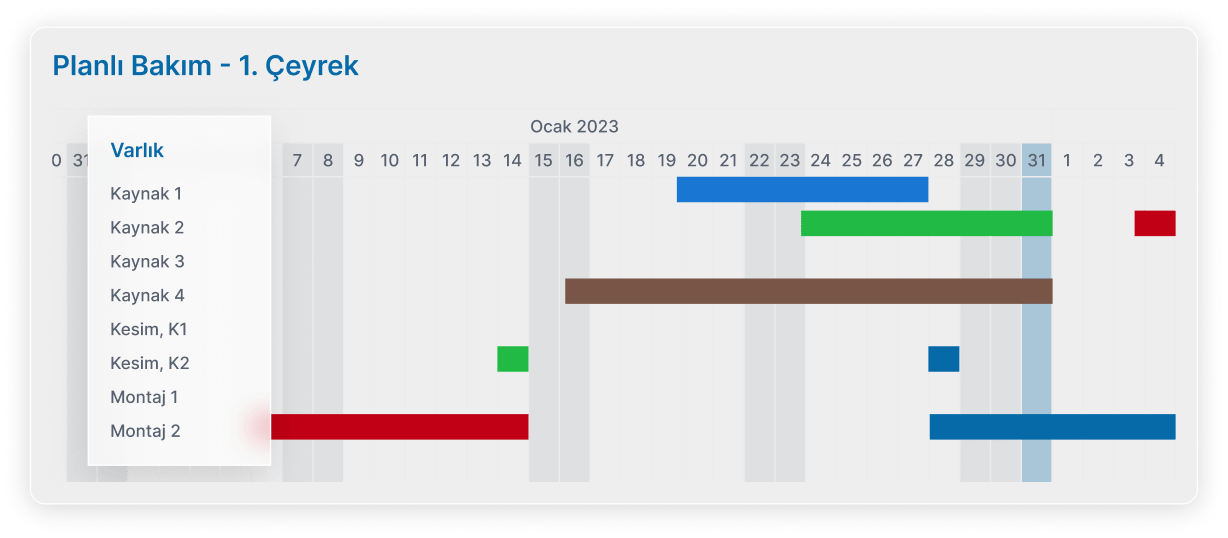
Maintenance Plan
FlowMio allows you to create detailed maintenance plans for your equipment. Time-based, counter-based, or condition-based periodic maintenance is planned in advance, minimizing breakdown risks. Maintenance dates, responsible teams, and required spare parts can be defined in the system, thus ensuring an uninterrupted production infrastructure.
Integrated Scheduling
FlowMio allows you to manage production, maintenance, and quality processes in an integrated manner on a single schedule. Conflicts and resource collisions are analyzed and alerted by the system in advance. This increases inter-departmental coordination and ensures adherence to planning.
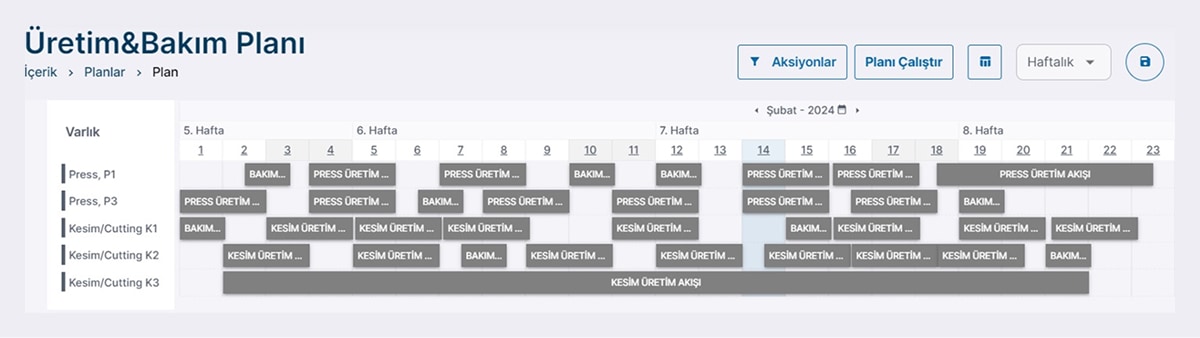
Quality Plan
Product-based, operation-based, or customer-based quality plans are defined, configuring the necessary checks for each production step in advance. Details such as which measurements to take, how often, and by whom are clarified. This planning prevents non-standard production and makes the quality assurance system sustainable in the digital environment.
Dynamic Field/Line Scheduling
Production lines in the field can be replanned based on real-time data. The system automatically updates the schedule according to potential delays, downtimes, or sudden order changes in production. This enhances agility on the production line and minimizes waste.
OHS Plans
Occupational health and safety plans can be defined in the system on an equipment and process basis. Hazard classes, control measures, responsible personnel, and implementation times are integrated into the plans. Audit and improvement activities can be tracked according to this plan. Thus, the production process is carried out in compliance with employee safety.
Training Planning
Training to be assigned to employees in line with new equipment, process changes, or quality requirements can be planned through the system. It is determined which personnel will receive training, when, and on what subject, making tracking easier. It contributes to creating a compliant and conscious production team.
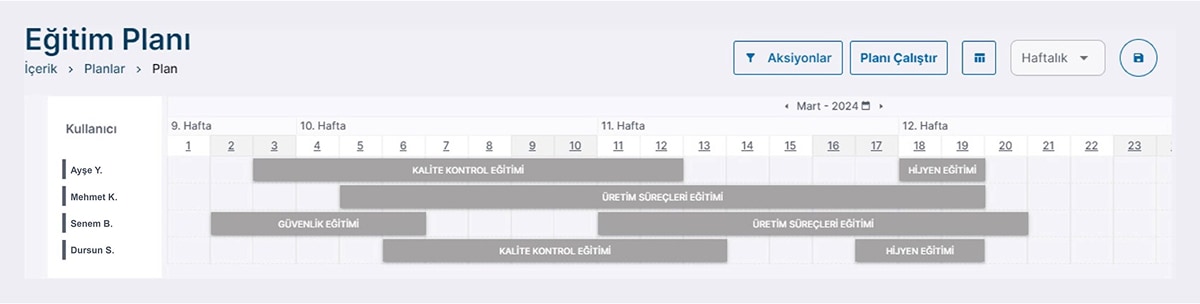
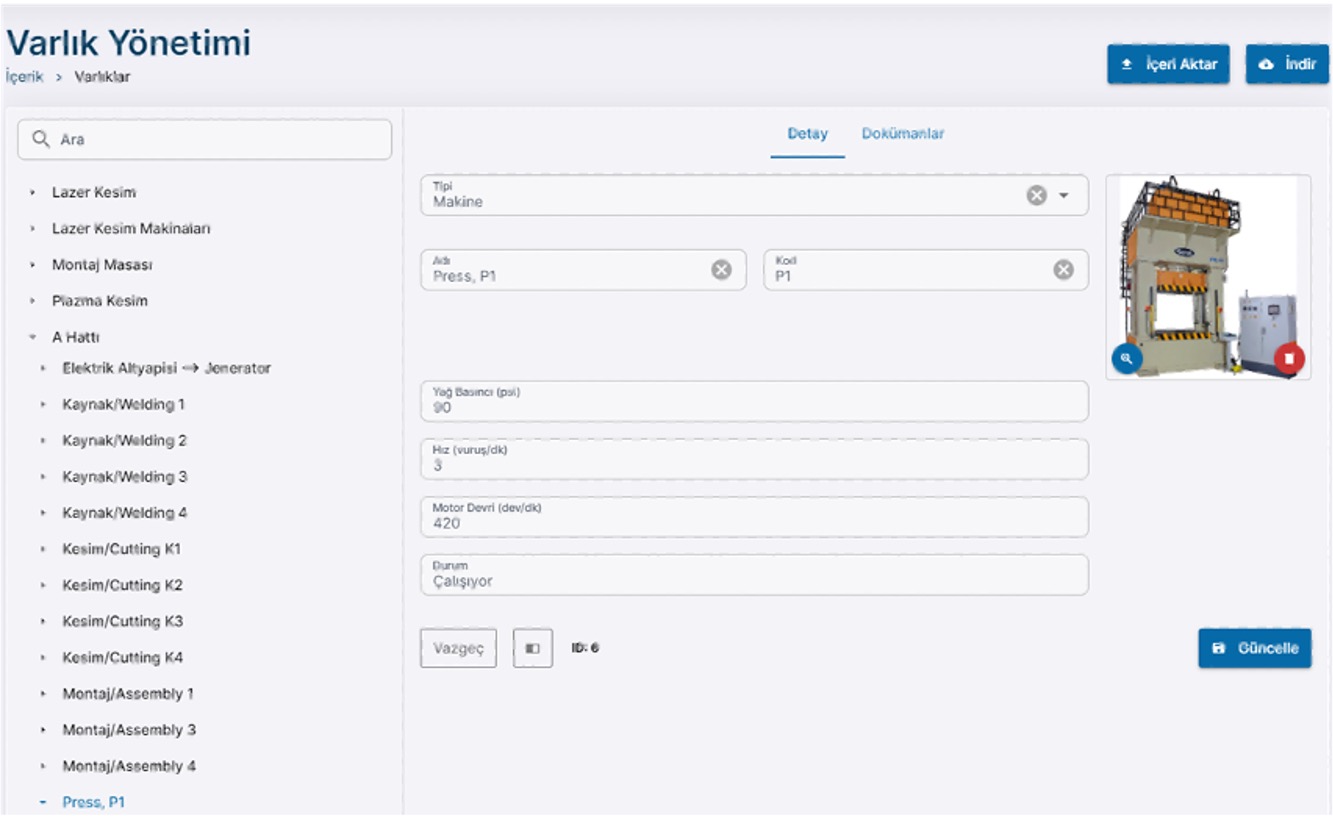
Flexible BOM/BOA/Route Definition
With FlowMio, Bills of Materials (BOM), Bills of Assets (BOA), and production routes can be defined flexibly. Alternative routes, substitute materials, and production variations can be created with scenarios in the system. This flexibility enables the production plan to quickly adapt to changing conditions.
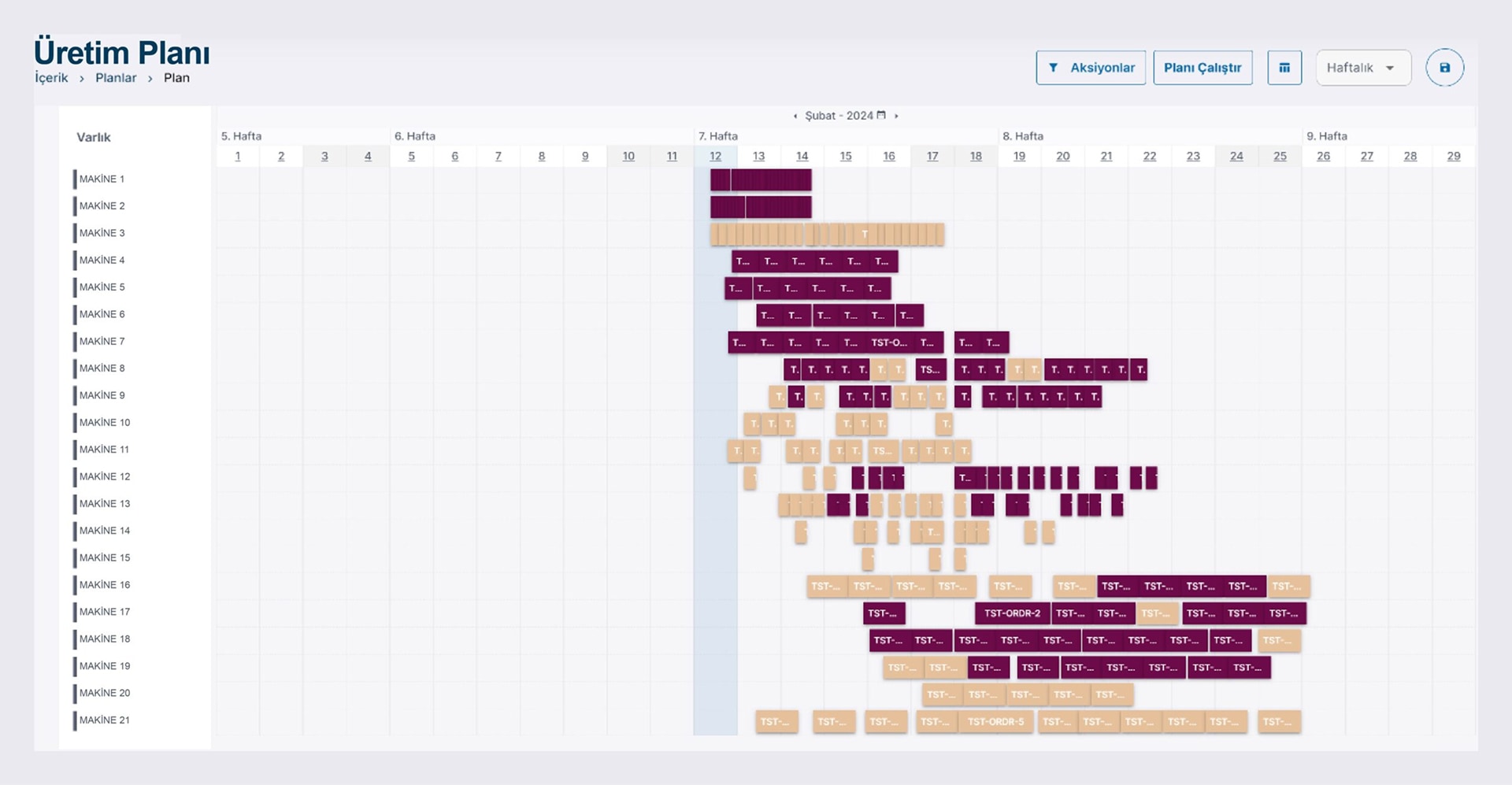
Gantt Chart
The entire production process is visually planned and monitored on a Gantt chart. All operations from order to shipment are located on the timeline. Delays, critical path analyses, and resource assignments are easily managed through this chart. This provides the planning department with a powerful control capability.
Internal Processes
Design your processes digitally, implement them quickly, monitor them instantly, and intervene when necessary. Stay in constant communication with your factory to maximize operational efficiency.
Supplier Risk Assessment
FlowMio’s advanced risk assessment infrastructure allows you to proactively identify critical weaknesses in your supply chain. A systematic evaluation is conducted based on numerous criteria such as suppliers’ delivery history, quality performance, certification status, and financial risk level. This makes supplier selection more informed while preventing potential operational disruptions. Alternative sourcing plans for high-risk suppliers can be easily made through the system.
OHS Management
FlowMio prioritizes occupational health and safety in production processes. All OHS processes, from risk analyses to emergency action plans, personal protective equipment tracking to field safety checks, are managed digitally. A proactive safety culture is established to prevent occupational accidents and diseases. Periodic OHS training, checklists, and implementation schedules are easily planned and monitored through the system.
Instruction Management
All operational instructions related to production, maintenance, quality, or OHS are centrally managed via the FlowMio platform. The system records which personnel viewed which instruction and when. Versioning and revision control eliminate the risk of using outdated documents. Operational standardization is ensured, preventing human errors and facilitating audit preparation.
Internal and External Audits
FlowMio digitizes internal quality audits and external certification processes end-to-end. Audit schedules are created, checklists are assigned via the system, and field audits are easily conducted with mobile devices. Non-conformities are quickly recorded, corrective actions are defined, and their follow-up is managed. This ensures continuous monitoring of compliance with international standards.
Copilot
Gain instant access to data with AI-powered insights and a command system via Copilot. Accelerate your decision-making processes and manage your operations smarter by increasing operational efficiency.
Factory Assistant
FlowMio’s Factory Assistant enables users to manage production processes using voice commands. Operators working on production lines can update production data, view reports, and receive new instructions by giving voice commands via their smartphones or mobile devices. This system allows operators to keep their hands free, thus ensuring a faster and safer production process. Furthermore, the Factory Assistant makes AI-supported decisions, offering speed and accuracy in production processes.
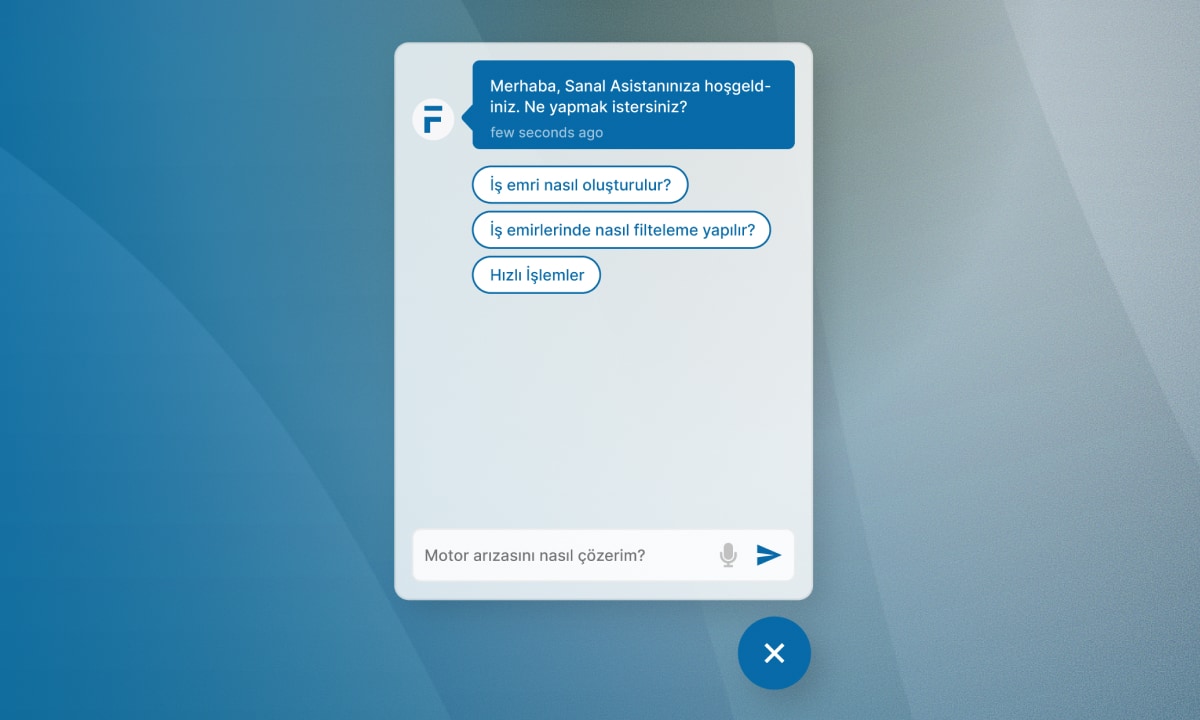
Analysis with Command System
FlowMio’s Analysis with Command System feature enables users to manage production processes more efficiently. Data is collected and analyzed using voice and text commands, making it possible to gain in-depth insights into every stage of the process. Thanks to commands, decisions based on real-time data can be made, leading to improvements in production processes. These analyses, which enhance operational efficiency, can be easily applied even in complex production lines and enable real-time action.
Reporting with Artificial Intelligence
FlowMio’s powerful reporting module allows you to create customizable reports for all production and operational processes. Data can be filtered, visualized, and detailed according to time intervals based on user needs. Real-time analysis of critical indicators such as production speed, quality control results, and maintenance processes supports strategic decision-making. Additionally, reports can be stored digitally and shared, providing access to all stakeholders.
FLEX modüllerini keşfedin
Discover FLEX modules
Üretim
Bakım
Kalite Kontrol
Planlama
Kurum İçi Süreçler
Ko-Pilot
Production
Maintenance
Manage operations smoothly by combining breakdown tracking and task planning.
Quality Control
Simplify quality processes with smart forms and automated checks.
Planning
Ensure tasks are completed on time by optimizing work schedules and management.
Internal Processes
Gain full visibility over operations with real-time dashboards.
Copilot
Accelerate decision-making processes with voice commands and AI insights.